SHORT NEWS
Changing shapes and materials using a 3D printer
Empa researchers have used a 3D printer to produce metal parts that are divided into surfaces with different properties. Among other things, they hope to apply this technology to improve the efficiency of electric motors.
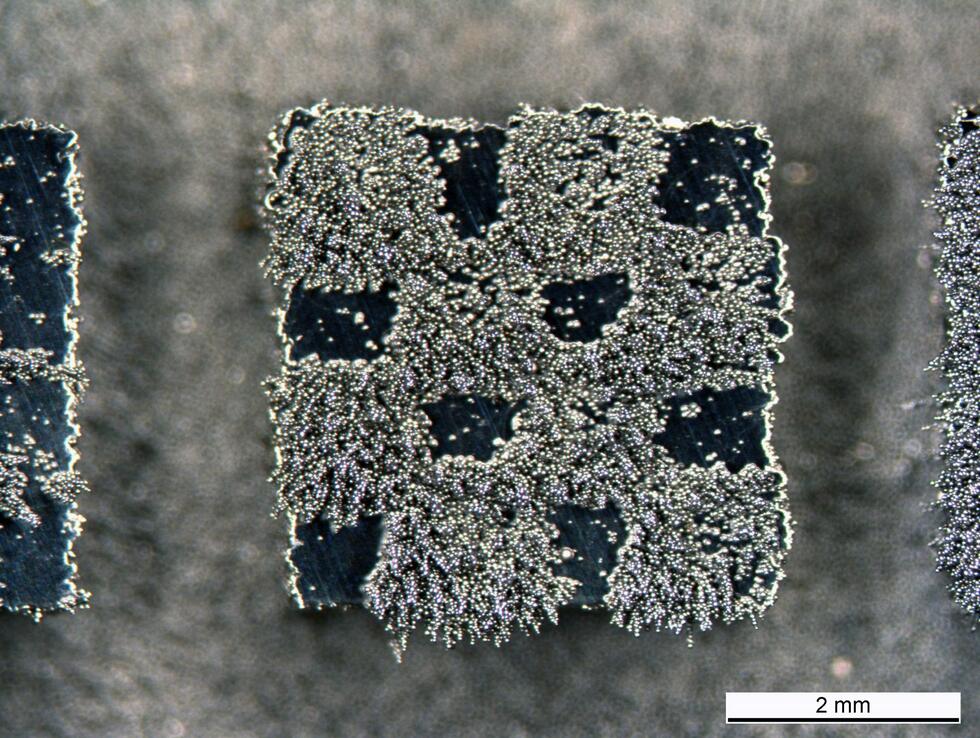
The 3D laser printer can achieve temperatures of more than 2500 degrees Celsius within just a few milliseconds. Not all alloys survive this intact; depending on the material, individual components are vaporized.
Researchers at Empa, the Swiss Federal Laboratories for Materials Testing and Research, have now transformed this weakness into a strength by using the 3D printer to produce parts with targeted, small-scale modifications to their properties. For example, they produced a minute chessboard on which some squares are magnetic and others are not – although the whole board is printed using the same metal powder.
This experiment, which may seem like a gimmick, could soon add a valuable tool to the methodology of metal production and processing, as the Empa team led by Ariyan Arabi-Hashemi and Christian Leinenbach announced.
Superior magnetic fields – more efficient motors
“When 3D printing metals, we can easily achieve localized temperatures of more than 2500 degrees Celsius,” Christian Leinenbach explained. “This allows us to vaporize different components of an alloy in a targeted manner – for example manganese, aluminum, zinc, carbon and more – and thus change the localized chemical composition.” The method is not limited to stainless steel, but could also be applied to many other alloys.
The researchers are convinced that the ability to produce alloys with micrometer precision in a single component could also prove helpful in the design of new, more efficient electric motors. “For the first time, we now have the possibility to construct the stator and rotor of the electric motor using magnetically finely structured materials in order to make better use of the geometry of the magnetic fields.”