Industrial Metaverse
It's here: the parallel world of industry. What are the benefits of the Industrial Metaverse? And where does development stand? Urs Reimann, Head of Digital Transformation at Bystronic, provides answers.
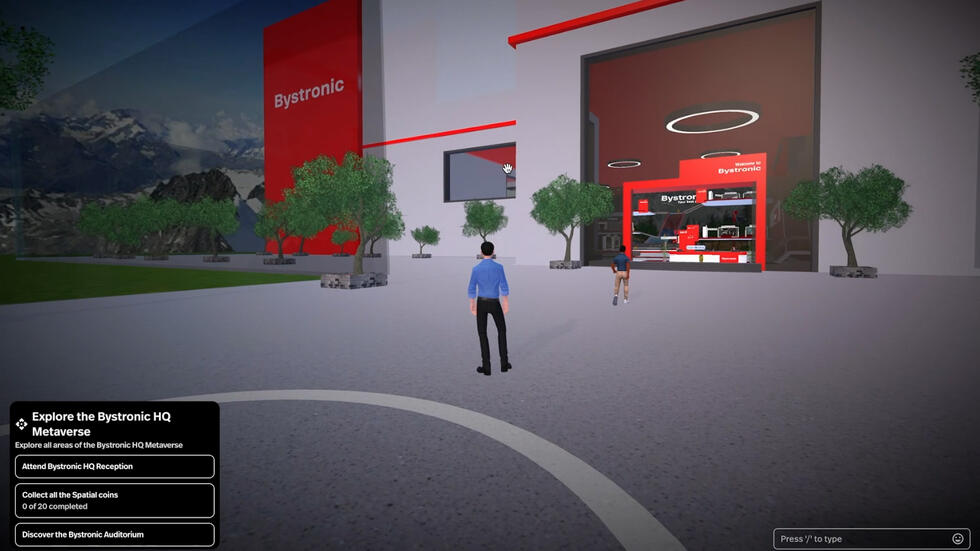
1989, Seattle: Sci-fi author Neal Stephenson is writing his novel "Snow Crash". In it, people interact in a virtual world, spending their free time there, trading or presenting their art. Special glasses provide access. Stephenson calls this parallel universe Metaverse. Today, over 30 years later, the metaverse really exists. The avatars in the "real" Metaverse pay with Bitcoin instead of "Quicksilver" and do not consume a drug called "Snow Crash", which makes them susceptible to manipulation. Otherwise, the metaverse comes remarkably close to Stephenson's vision.
A completely new digital society and economy in which people learn and work in a playful - "gamified" - way: The potential of the metaverse is enormous. The drivers behind this are tech companies such as Meta, but also the US games sector with companies such as Epic Games and Roblox Corporation. They all already operate their own metaverse platforms. However, more and more solutions based on computer-aided drafting (CAD) are currently coming onto the market. They serve the specific needs of industry and form a new development: the Industrial Metaverse. A warm welcome to you.
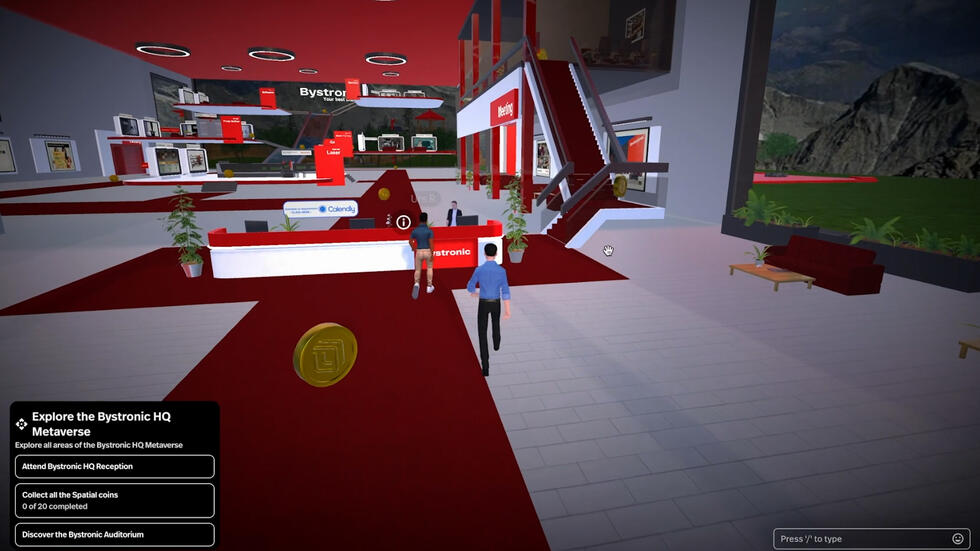
Urs Reimann, what is behind the industrial version of the Metaverse?
Essentially, it's about the virtual representation of existing factories. The avatars of real people can immerse themselves in these worlds, just like in the commercial metaverse.
How should I imagine such a virtual factory?
On the one hand, it is very realistic: the Industrial Metaverse is based on the CAD data of existing machines and systems. This allows users to zoom in down to the smallest screw. In addition, the machines continuously send their data to the metaverse. This data arrives there with almost no time delay. On the other hand, the data can, for example, be displayed completely differently than in reality. This makes it possible for people to spatially perceive what is happening on the machines.
Give me the 3D view.
Imagine this: Your avatar walks through the factory hall and machine data lights up on screens to the right and left: Temperature, speed, pressure. Or even better: there is a data cockpit where the data is immediately correlated and problem probabilities are calculated. So you no longer have to physically walk from machine to machine, read boring reports or look at static screens. In the Metaverse, you capture information better and faster, so you can react to problems more quickly and have fun at the same time. Data analysis becomes an experience.
What does the factory floor look like?
For example, futuristic or with floor-to-ceiling glass windows. It's better to work like that than in a gray building, isn't it?
I can imagine (I work in a newspaper editorial office).
Varied environments lead to better results. But the creative design of the working environment is more of a sideshow. The greater benefit of the Industrial Metaverse lies in virtually optimizing analog spaces or creating new spaces down to the last detail.
Like the data cockpit from earlier?
That's right. Another example would be a laboratory for remote collaboration that is equipped with everything needed for state-of-the-art product development: a 3D printer, comprehensive material libraries, presentation rooms. All of this is available in the Industrial Metaverse, absolutely space-saving and free of charge. As you can see: The concept has the potential to revolutionize innovation and efficiency in industry.
In addition to remote collaboration and data analysis, what other areas of application are there?
Prototypes no longer need to be physically built, for example. Or industrial processes can be realistically simulated in order to predict and optimize the effects of changes. Machines no longer have to be transported halfway around the world for presentations. And marketing departments can quickly and easily obtain high-resolution images of machines from every conceivable angle.
The revolution in brand loyalty: NFTs
Non-fungible tokens, or NFTs for short, play a crucial role in the (industrial) metaverse. NFTs are digital assets, for example digital art, land or collectibles. They regulate unique ownership and confirm the authenticity of an asset. However, NFTs also have the function of tickets or rewards in the metaverse. Industrial companies can take advantage of this: For example, NFTs give customers exclusive access to digital experiences, content or events. NFTs also promote community building: they encourage users to take part in special activities and get involved in groups and communities that share their interests and values. Customer and brand loyalty at its best.
What is the biggest benefit for Bystronic?
We originally introduced the Industrial Metaverse to reduce the time and effort required for our machine training courses - a pain point for many industrial companies. Previously, we had to create countless PDFs and videos for the training courses and adapt them again and again, as the machines are constantly being further developed. In Metaverse, the update is done automatically based on the latest CAD data. In addition, the training courses can be made much more entertaining - even directly on the machine with the help of AR (augmented reality).
How does this work?
The employees wear AR glasses, where the instructions are displayed at the top left, for example. At the same time, they carry out the steps in practice instead of working through theoretical documents. Like the commercial Metaverse, the industrial version also combines virtual reality with physical reality, thereby expanding it.
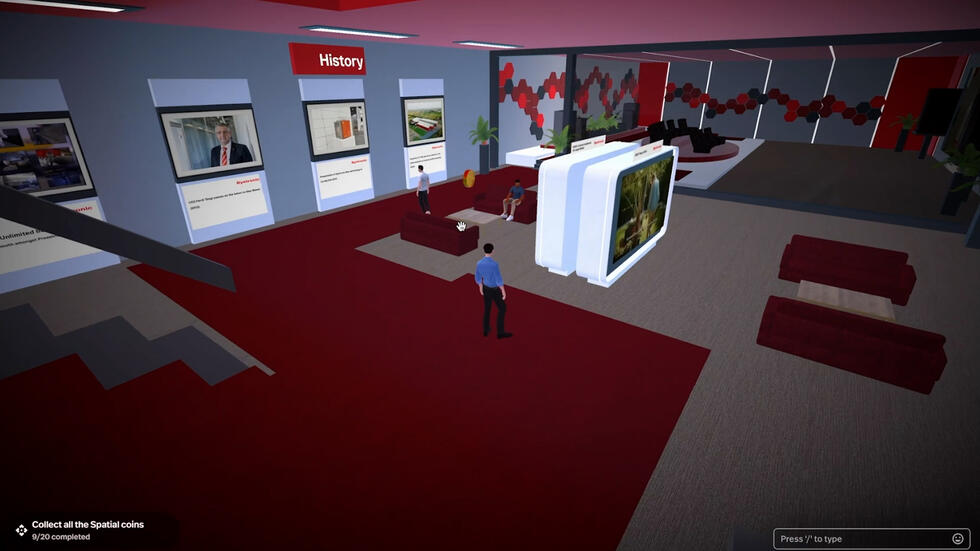
The metaverse and Web 3.0
The pure information Internet is a thing of the past: now comes Web 3.0, of which the commercial and industrial metaverse are components. The aim is to make virtual experiences feel like real life. But there is much more to Web 3.0: it is based on blockchain technology and is controlled decentrally. This is because it should no longer be controlled by anyone, not even the big tech companies.
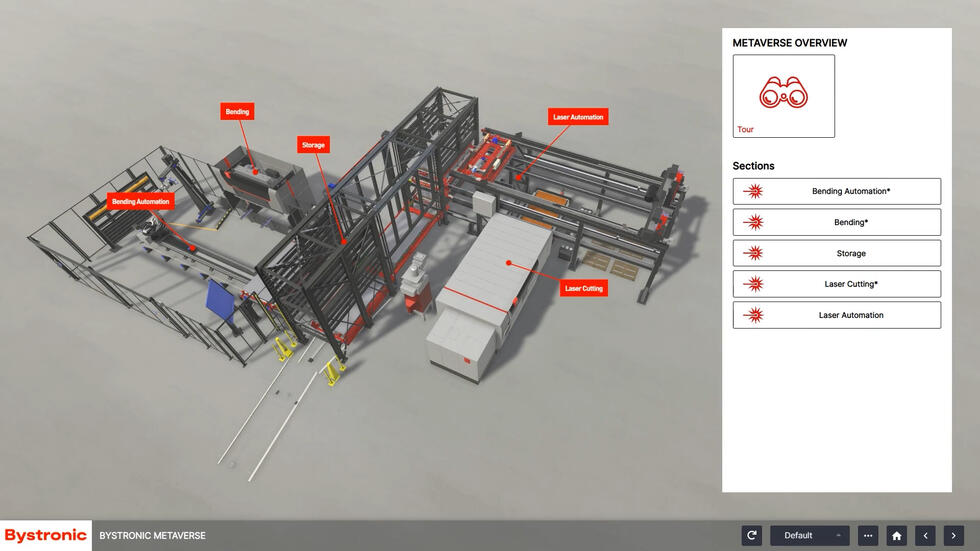
Let's stick to the practical side: How does access to the Industrial Metaverse work?
Users log into the Metaverse platform via PC or cell phone. To navigate the platform, they either stay on these devices or use AR glasses or VR glasses, depending on the application. This allows them to immerse themselves completely in the virtual world (virtual reality, or VR for short).
And how widespread are metaverse solutions already in the industry?
This process is really picking up speed right now. The technologies on which the industrial metaverse is based have made great progress in recent years: AR, VR, the Internet of Things (IoT), which networks machines and devices with each other, and artificial intelligence. What's more, the technologies are now compatible with a wide range of hardware and software systems. This has made the introduction and operation of platforms uncomplicated and relatively inexpensive. And: there are more and more platform solutions based on CAD. Commercial metaverse platforms such as Sandbox or Roblox are not suitable for industry; they are not detailed enough.
To sum up: the industrial metaverse heralds a new era for production companies. Are there also risks?
Quite a few. The biggest challenge is certainly the protection and security of data - as with most digital innovations. But AR and VR glasses also have their pitfalls: if they are not adjusted ergonomically, they can damage the eyes or cause headaches. The industrial metaverse is also a double-edged sword when it comes to sustainability.
Because of the high energy consumption?
That's right. On the one hand, digital representations and simulations save a lot of material and energy. On the other hand, all the computing processes and data transfers consume a lot of electricity. And resources are also needed to manufacture the glasses. It is therefore important to find sustainable solutions, for example by using renewable energies and efficient software algorithms. Because one thing is certain: the (industrial) metaverse cannot be stopped.
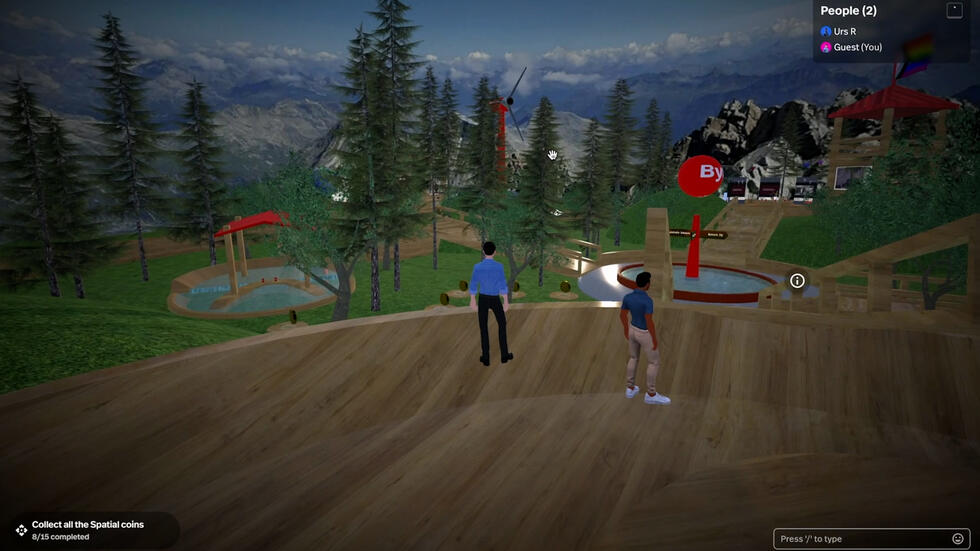