Structure that creates stability
The architect and structural engineer Francesco Ranaudo is researching how precast concrete ceiling slabs can be manufactured thinner, lighter, and in a more sustainable way. To achieve this, he is utilizing both 3D printing processes and techniques of master builders of old.
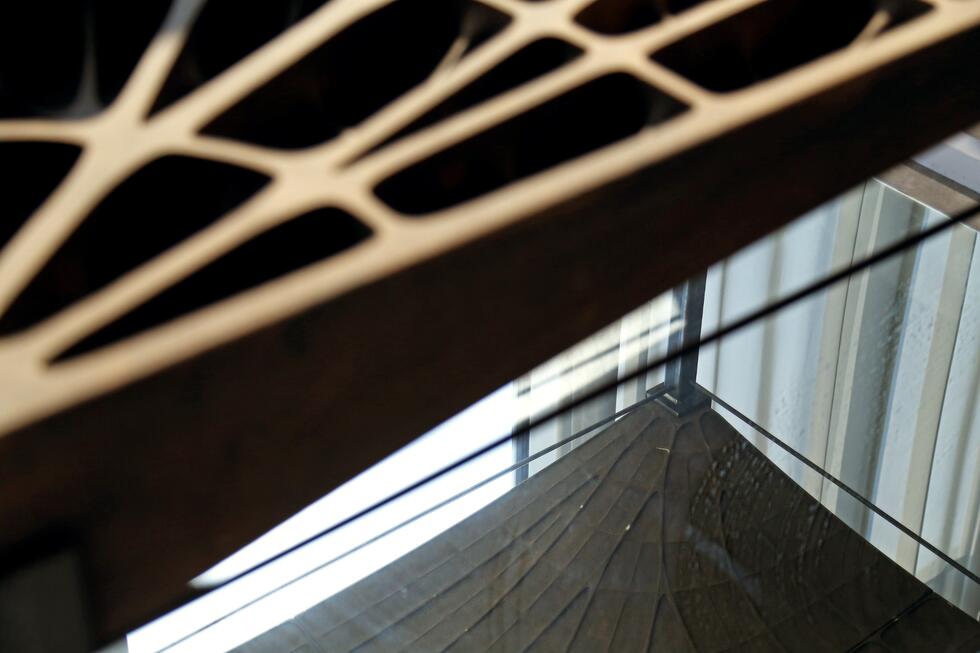
“When it comes to battling climate change, everyone first focuses on flying,” says Francesco Ranaudo shaking his head. Flying less certainly doesn’t hurt, admits the Italian-born researcher who is currently enrolled in a doctorate program at the Swiss Federal Institute of Technology (ETH) in Zurich. But architecture offers a considerably more potent leverage to reduce carbon emissions, Ranaudo emphasizes.
Francesco Ranaudo explains: “The United Nations forecasts a population growth of roughly 2 billion by the year 2050. In order to ensure all these people have a roof over their heads, we have to build residential space on the scale of New York City every month. A new New York – every single month!”
This is an impressive illustration of what impact widespread optimizations can have. And this is where the architect and structural engineer is tackling the problem. In his role as a doctoral candidate at the Institute of Technology in Architecture, and as a researcher on the Block Research Group and with the National Center of Competence in Research on “Digital Manufacturing”, his goal is to improve building designs while reducing costs and emissions. His focus: precast concrete slabs for ceilings.
Climate killer concrete
Concrete – a mixture of water, cement, and sand or gravel – is harmful to the environment. Among other things, the emissions generated during the sintering of the cement are a major environmental issue. The United Nations Framework Convention on Climate Change (UNFCCC) estimates that cement production is responsible for 5 to 6 percent of global human-generated greenhouse gas emissions.
The addition of sand is also an issue because sand is a finite resource. In the case of reinforced concrete, the emissions generated during steel production are an additional factor: Depending on the source, this is estimated to be around one to two tons of carbon dioxide per ton of raw steel. In high-rise buildings, which have to withstand greater forces due to their own weight, the ecological component is particularly important: ultra-high resistance, reinforced concrete contains a higher proportion of both cement and steel.
Recycled concrete, in which a part of the aggregates – i.e. sand or gravel – is replaced by existing crushed concrete, has a more favorable ecological footprint. However, this reduces the load-bearing capacity of the material. Consequently, new concepts are called for in order to be able to construct buildings that are both structurally sound and sustainable. According to Francesco Ranaudo, “strength through material” is no longer state-of-the-art. Nowadays the maxim is: “strength through geometry”.
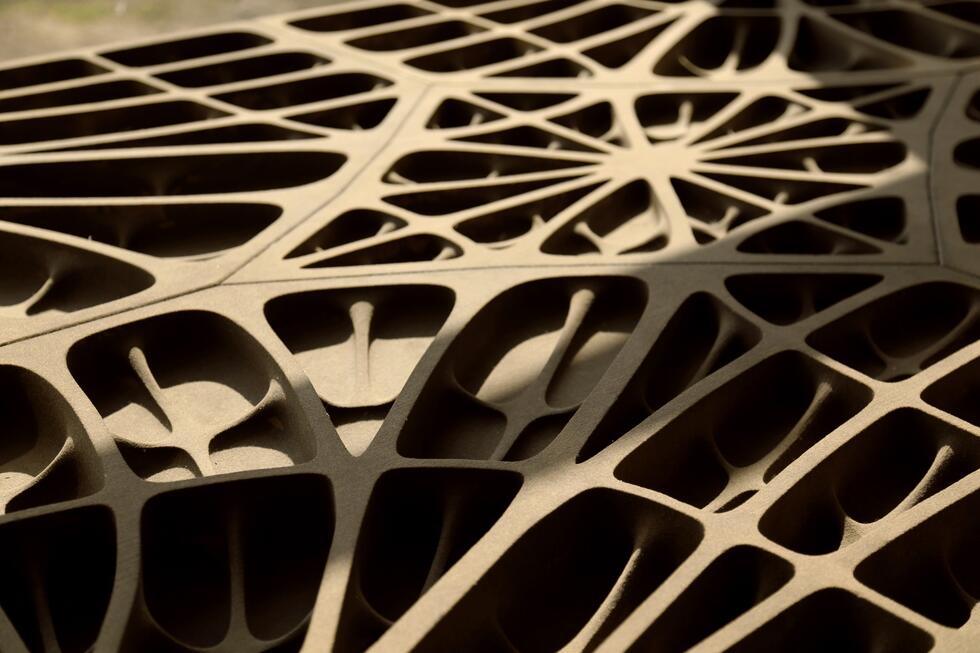
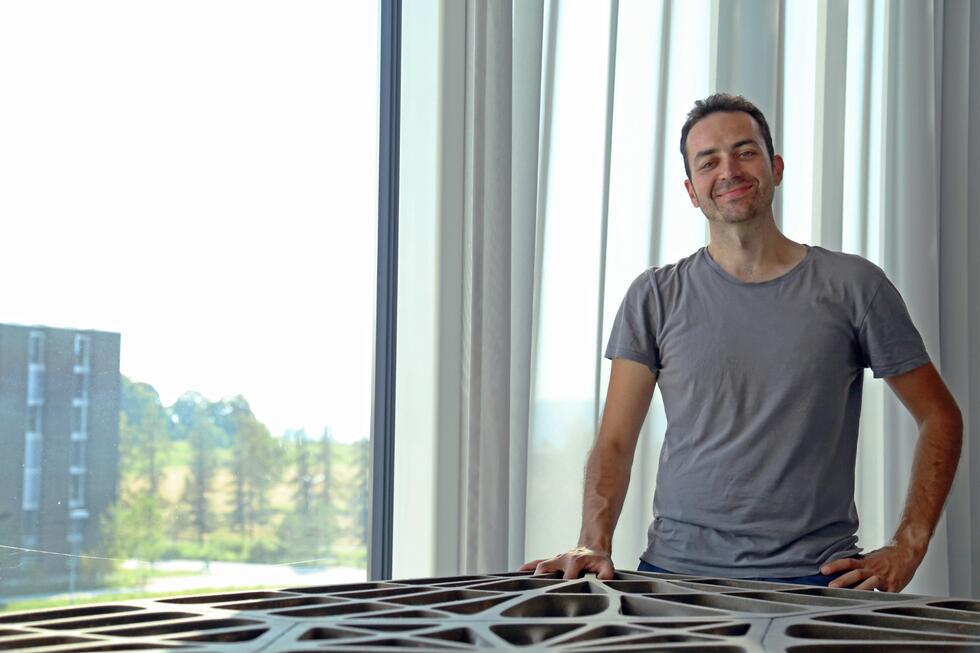
Inspired by master builders of old
Francesco Ranaudo shows what he means by this during a guided tour of the ETH institute. On the upper floor of the building is a prototype of the concrete ceiling that he is currently working on. With its airy ribbed structure, the approximately five square meter large and ten centimeter thick slab looks a bit like an ornate component of a Gothic cathedral. “This appearance is no mistake, our design is actually inspired by the master builders of old,” he says. “Because they too were forced to rely on structure to ensure the stability of their buildings.” They did not yet have access to the possibilities of modern materials.
On the one hand, the geometry of the slab is designed to minimize the use of resources; on the other, the ribbed structure and its slight arch shape ensure that the loads acting on the ceiling are evenly distributed and diverted from the center to the corners. Thus, forces that more environmentally friendly materials such as recycled concrete could not withstand are prevented from occurring in the first place.
As a result, there is no need for reinforcement in the conventional sense. Only at the corners of the ceiling slab, a steel support structure provides additional stability. So steel is required after all? “Yes”, Francesco Ranaudo admits, “but much less than with conventional reinforced concrete”. And what is more: It is an external support structure – not like rebar reinforcement into which the concrete is poured. This makes it much easier to separate and recycle the metal after use.
Thinner, lighter, more ecological
The ceiling withstands the loads – even though it is thinner and lighter. “This saves about 50 percent of the material and between 30 to 40 percent of the total weight of a building,” the researcher explains. For a 20-story building alone, the savings potential is enormous. “I ran some calculations for an interested party,” says Francesco Ranaudo. “Compared to conventional concrete ceilings, our concept would save 1208 truckloads of concrete. And we could eliminate the need for rebar that if stretched out would reach all the way from Zurich to Brussels – more than 600 kilometers.
The fact that the ceiling is not only lighter, but also thinner, becomes all the more important the more floors a building has: If you save approximately 10 centimeters per floor, this results in an additional floor for buildings with 25 or more floors – without increasing the height of the building. “Although the vault shape means that a little room is lost, this is limited to the corners and walls – space that people rarely use anyway,” the researcher explains.
We could eliminate the need for rebar that if stretched out would reach all the way from Zurich to Brussels – more than 600 kilometers
On the first floor of the institute, another prototype of the ceiling is currently curing. There is not much to see yet, because the slab is still embedded in its formwork. Francesco Ranaudo explains the ingenious details behind it: “The pipes for heating and cooling are integrated directly into the slab, which eliminates the need for additional installation layers, which would otherwise add to the overall thickness of the ceiling. In addition, the pipes are designed in such a way that the surface area available for heat exchange is maximized.”
The ventilation has also been optimized in cooperation with the “Digital Building Technologies” and “Architecture and Building System” research groups: Parts of the formwork were 3D printed, giving the underside of the concrete element a grooved structure. This structure creates micro-turbulence and improves air circulation.
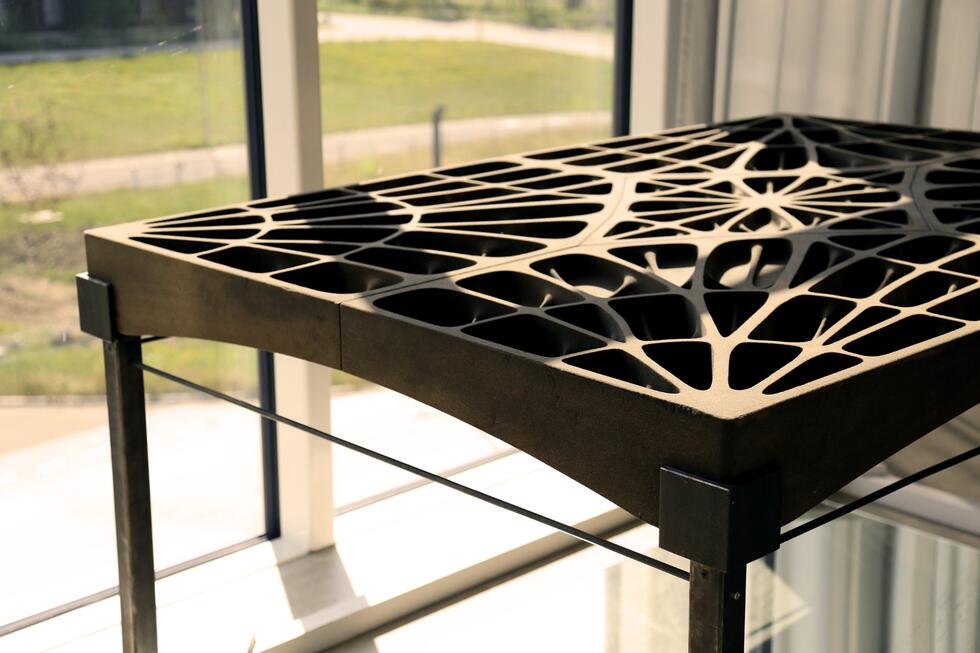
Working towards market maturity
A first test of the concept is about to begin. The slab is part of the “HiLo” project run by Empa, the Swiss Federal Laboratories for Materials Testing and Research. “HiLo” is a two-story building near Zurich, which serves as a research and innovation platform for new lightweight construction methods. Construction began in the summer of 2019, and the ceilings are due to be installed this fall.
“If we apply NASA’s Technology Readiness Levels, the ‘HiLo’ project is roughly equivalent to an astronaut who is training in an indoor pool – i.e. level 5 or 6,” explains Francesco Ranaudo. In order to reach level 9 – the maximum – there is still work to be done, in particular in the field of certifications and standards.
And it is absolutely crucial to convince potential users and the general public of the concept: “Building with conventional materials and processes is comparatively simple and fast. This has made us rather complacent. And this will only change if the factor of resource efficiency becomes just as important as the time factor.”
Digital manufacturing
The “Digital Manufacturing” National Centre of Competence in Research (NCCR) is funded by the Swiss government and investigates innovative planning and construction processes in the field of architecture – among other things with the aim of closing the gap between digital technologies and the physical construction process. This includes digital design and manufacturing processes and their synthesis in innovative new technologies. Various academic disciplines work together within the NCCR: architecture, structural design, electrical engineering, mechanical engineering, robotics, materials sciences, and computer sciences.
Photos and written by: