The house from the 3D printer
Open design ideas instead of rectangular geometries: Houses from the 3D printer not only look different from conventional buildings. Suppliers from the industry also promise that the technology is faster and more resource-efficient. But, Is that really true?
Colorful game figures, artificial hip joints, deadly firearms: 3D printers translate almost every digitally conceived form into reality. And the technology has been growing rapidly for years. Now it could change the construction industry from the ground up. To this end, partners from industry and science are coming together worldwide to print entire buildings. There are also model projects in the DACH region: For example, the Swiss research association's "DFAB House," which was built using robots and 3D printers. Austria's first printed office complex is in Hausleiten, and Germany's first 3D-printed apartment building is in Beckum. Ina Scharrenbach, the construction minister responsible for the project, said at the opening that it would "generate positive pressure in the construction industry."
"Just recently, the United Nations estimated that in 2021, more than one-third of global CO2 emissions were attributable to the use and construction of buildings."
And that is long overdue. Because the construction industry needs to change. It is a major C02 sinner. For climate change. Just recently, the United Nations estimated that in 2021, more than one-third (37 percent) of global CO2 emissions were attributable to the use and construction of buildings. Concrete production alone is responsible for around ten percent annually. And the trend is upward.
A rapid rate of urbanization is primarily responsible for this. More and more people are moving from the countryside to the city - and need living space. Dirk Messner, President of the German Federal Environment Agency, recently said: "The population in urban areas will double to seven billion people in the next 25 years. If we were to build the buildings for that, as we have been doing, it would use up our remaining CO2 budget by the 1.5-degree target." Just for this housing. Mobility, energy and other sectors are not even taken into account. If the construction industry simply continues as before, it will clearly miss the goal of the Paris climate agreement: to limit the rise in average global temperature to well below two degrees Celsius above pre-industrial levels.
Round corners - the hallmark
"The time is ripe for transformation. After all, we are still building today as we did 60 years ago," says Christoph Gehlen . He is a professor of materials and materials testing in construction at the Technical University of Munich and has high hopes for 3D house printing: "Compared to conventional construction, not only could material use be reduced, but also CO2 emissions and construction time." Conventional building means putting up a formwork, filling it with concrete and inserting grids made of steel - as has been done on almost every construction site for decades. If Gehlen has his way, that's where building printers would come in the future. "Technology could take over heavy work, making up for the shortage of labor." And not only that: "If we technologize the industry, that would certainly provide for new blood," says the 56-year-old. Because that has been dwindling for a long time.
"Compared to conventional construction, not only could material use be reduced, but also CO2 emissions and construction time."
Then there's the promise of customized architecture: thanks to printers, there would be no need to build square. "We can find new designs and geometries," says Gehlen, alluding to the "round corners" - the hallmarks of printed buildings. They occur because the viscous building material must be printed evenly. Otherwise, the walls will end up with different thicknesses. To avoid this, corners become tight curves.
The most widely used process at present is the depositing process, extrusion. It works like this (there are also others, see Infobox 2): A nozzle hangs from an axis that can move freely in space. A special concrete mixture flows through it at the push of a button. What looks like gray toothpaste hardens quickly and grows layer by layer to form a wall. What is special is that each layer can be made of a different material, with different properties. Currently the most widely used machine can create buildings up to ten meters high and nearly 15 meters wide. The length is flexible. This is due to the fact that the structure with the nozzle, the printer housing, so to speak, can be expanded in a modular way. The nozzle prints a layer of wall at up to 50 centimeters per second. That sounds fast, but the net printing time is only a fraction in the pilot projects. It takes much longer to prepare the site, set up the printer, maintain the machines and troubleshoot, which only a few experts with specialized knowledge can do.
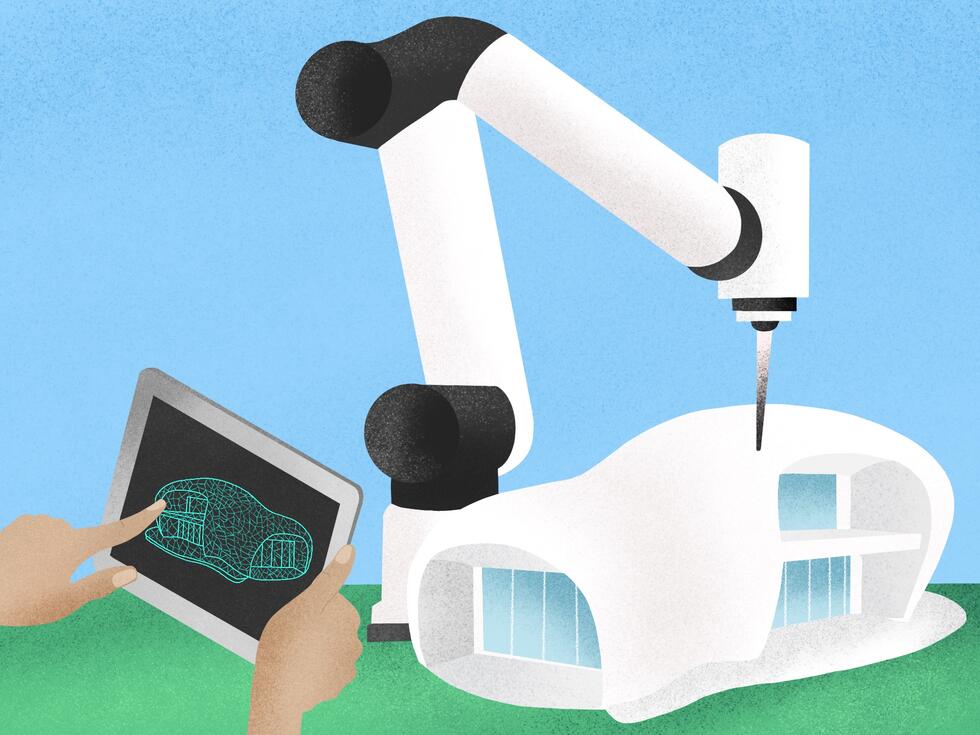
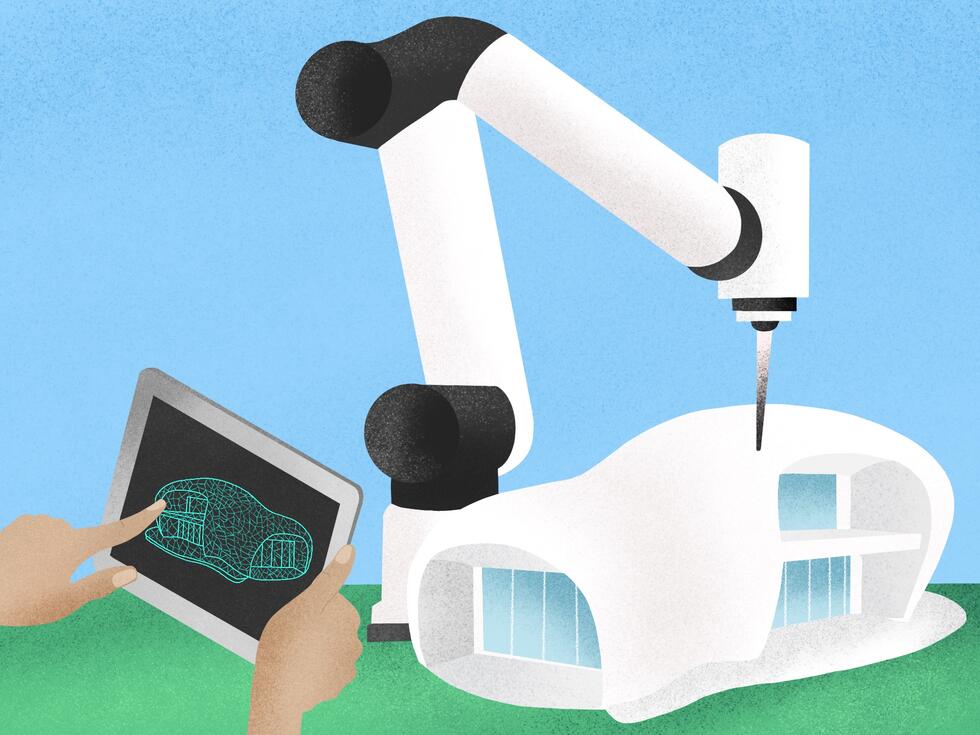
What can printed concrete do?
Gehlen is nevertheless an advocate of house printing - and a longtime expert. He accompanied the 3D house in Beckum on the science side and can therefore explain what the technology can do like no one else. Since 2013, he and his team have been working on making concrete printable in workshops at Munich University. They quickly discovered that conventional products were not suitable. But cement was also to form the basis for the pressurized concrete, since it is available everywhere. "We tried a lot of canary ideas." What he means: colorful and crazy additions. For example, they added wood chips. With moderate success. "We learned a lot about incompatibilities of different materials." For example, that ingredients in organic wood prevent mineral cement from hardening. Over time, however, they found recipes that liquefy concrete sufficiently and make it pumpable so that it can pass through the pressure hose and still be dimensionally stable and quick-drying a short time later.
"We learned a lot about incompatibilities of different materials."
At the house in Beckum, Gehlen was able to show what printed concrete can do. "We did the approval tests for the building inspectorate," he says. For example, they conducted weather resistance studies. To do that, they exposed printed concrete models to extreme conditions. "We put them in water, froze them and thawed them," Gehlen says. "Over and over again." That's how they simulated seasons. Then they looked under a microscope and ultrasound equipment: How has the building material aged? Hardly at all.
The compressed concrete also passed all static tests. Each individual component is, they say, sufficiently "stable." Yet even Gehlen feared that, compared to conventional stone walls, printed walls would withstand much less load. The challenge lies in the timing: Because layer upon layer is printed, a joint is created in between. If the concrete flows too slowly, "cold joints" are created. Cold joints. Then the concrete strands that lie on top of each other do not adhere as well. A new strand must therefore not be applied too slowly - but not too quickly either. Otherwise, the concrete underneath will deform because it is not yet hard enough. In Beckum, new courses were applied after seven to twelve minutes, so there were no cold joints. In comparison, the printed walls achieve around 80 percent of the stability of conventional walls.
"House pressure is not the solution for the construction industry."
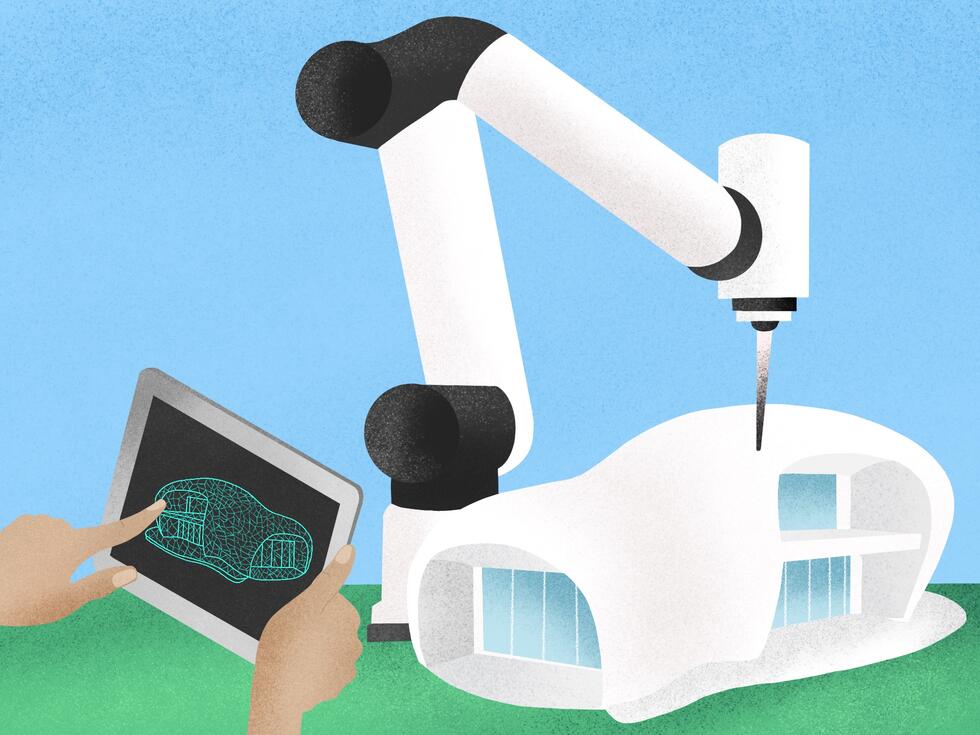
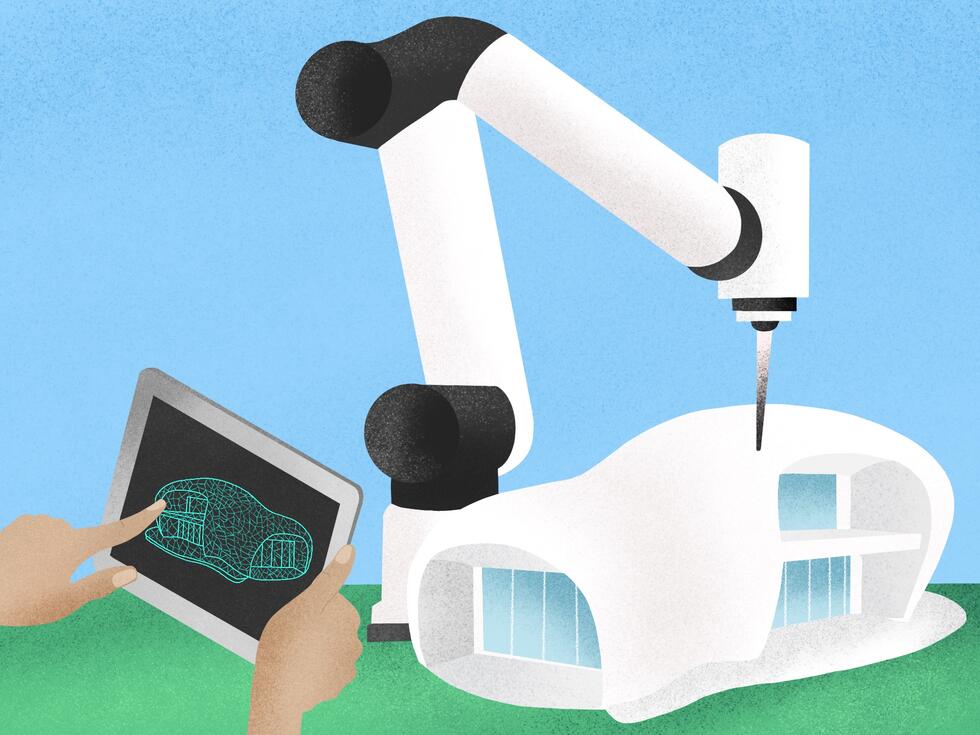
Gaps with function
At the same time, printed walls can do more. "Because we can, for example, print resonance bodies that absorb sound into the surface," says Gehlen. "Or we can cut out functional voids in the walls." Media could be laid more easily through them or warm air could be conducted to heat the building. The biggest advantage, however, is that if the wall consists of only one material, it can be recycled more easily. Today, walls consist of glued or screwed material sandwiches, each layer having a different function. Therefore, the components can only be separated again with a lot of effort and money - in practice, this almost doesn't happen. "It would be a contribution to sustainability that single-variety printed walls could be more easily returned to a building cycle," Gehlen says.
But this is where the materials professor sees the biggest contribution of home printing to sustainability: "We can save a lot of material on ceilings and walls. Because we only print what we need." In conventional buildings, he says, walls are the same thickness everywhere. Yet that doesn't have to be the case for the load-bearing capacity, he says. "That's why resources are lost. 3D printing lets us build much more purposefully." That saves up to 50 percent in material, and even more for some components. Even if all the components were just a little slimmer, that would yield a lot of leverage, he said. "Houses, tunnels, bridges: If you subtract 30 percent everywhere, it's significant," Gehlen says.
"It's certainly not going to be a complete replacement for conventional building."
Despite everything: House pressure is not the solution for the construction industry. At least not yet. This is also the direction taken by the rating on the "Technology Readiness Scale" (see Infobox I): out of 9 levels, the still young technology stands between 6 and 7. Translated, this means that house printing works "in the actual application area" and the machines "approach a finished product". A review of eight model projects in eight countries also comes to a similar conclusion. It says: "While the number of model projects is increasing rapidly, they have so far tended to pursue the goal of demonstrating potential and not necessarily achieving it." It is these (theoretical) possibilities that also convince Gehlen. He says people will build "leaner, faster, more varied and perhaps cheaper," "making house printing the technology of the future." But, "It's certainly not going to be a complete replacement for conventional building."
And then there's a key problem: the building material. Liquid concrete has so far relied on very fine-grained formulations; instead of gravel, it needs sand. The smaller the grain, the more glue must be used. "And the glue consists of water and a lot of cement. That's why CO2 emissions are still far too high," Gehlen says. "If I had to give an assessment of the technology now, it wouldn't be pretty." He sees huge potential, and it's probably only a matter of time before emissions can be reduced or avoided altogether. "But so far, it hasn't," Gehlen says.
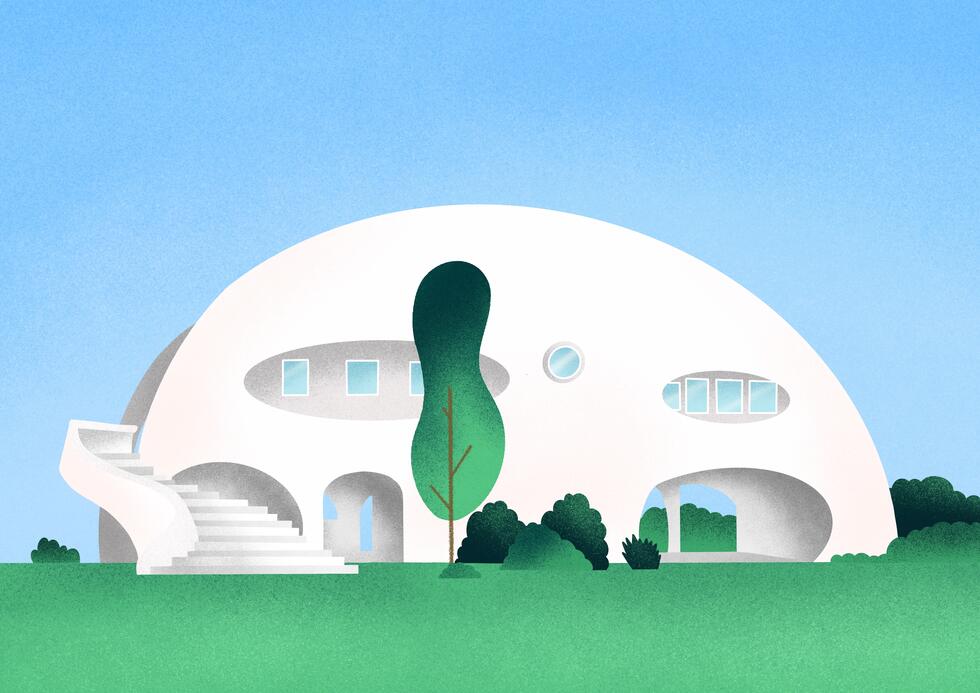
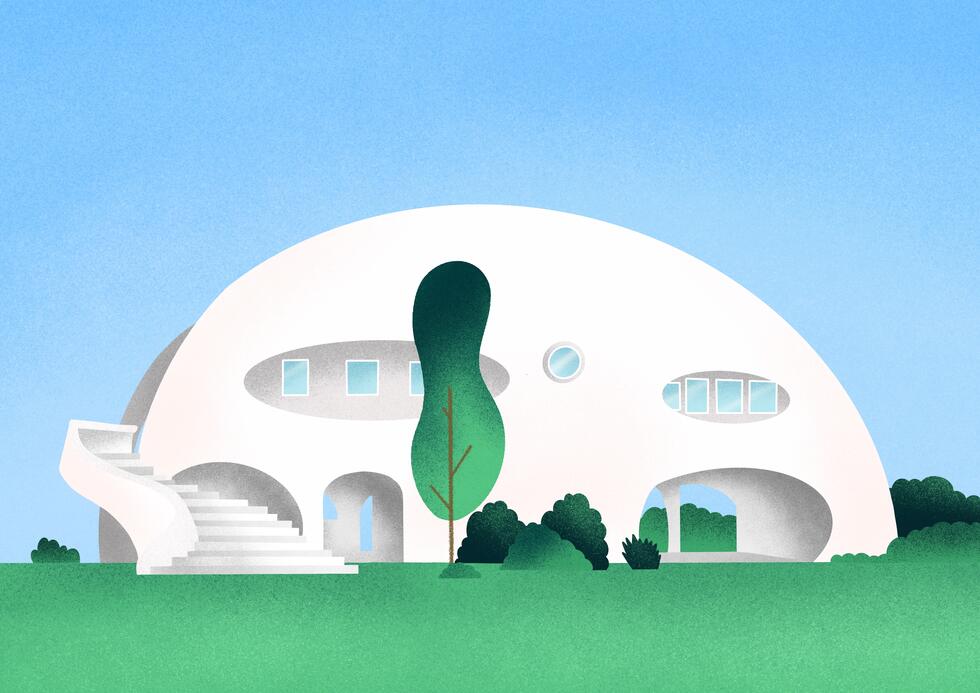
Nothing more than "a nice gestalt"
Annette Hillebrandt comes to a similar conclusion. She holds the chair of building construction at the University of Wuppertal, where she researches circulation potentials in building construction. She is not involved in the current house printing projects, but is observing the development. For her, 3D houses are not a sustainable solution - on the one hand because of the far too high cement content in liquid concrete. "But there is also wood 3D printing. There, however, plastic is added as a binder, which prevents subsequent composting," she explains. That's why she can't see anything to gain from the technology, except for a nice design.
She also makes two other points. The first: "Even if material is saved on walls and masonry, solid construction wastes resources compared to modular and prefabricated skeletal buildings." Modular construction is also more flexible for change, he adds.
The second reason runs deeper: Hillebrandt believes new construction is generally unsustainable. Referring to Germany, she says, "We have stagnating population figures. That's why we should make do with the existing building stock." Sure, it could be converted or "spruced up." But, "We only have a small CO2 budget left if we want to meet the climate targets and contain global warming to 1.5 or 2 degrees." That's where every unnecessary kilogram of CO2 is too much, she says. She says, "Yes, 3D printing is pretty. But it sends the wrong signal in this time of climate change and increasingly scarce raw materials."
Infobox 1
A review paper examined different construction projects from eight countries, including the house in Beckum. According to the authors, the three-dimensional house print now has a 6 to 7 on the "Technology Readiness Level" (TRL) scale. This ranges from 1 to 9 and thus assesses the maturity of a technology. It was originally developed by the U.S. space agency NASA to answer the question: Is a development reliable enough to be used in rockets and satellites? However, the scale is now used in many research fields to describe the stage of development of a technology from its foundation to the finished product. Level 6 means "prototype in deployment environment," Level 7 "prototype in use." This means that 3D printing has been able to demonstrate that it "works in the actual field of use" and approaches a finished product. The step from level 6 to 7 is an important one, because it connects the research & development with the pilot application and thus leads out of the lab and into the application "in the field".
Infobox 2
In addition to extrusion, research is also being conducted on the "shotcrete" process. In this process, concrete is not forced through a nozzle but shot at high pressure. This increases the construction speed and ensures better mixing of the layers. Also, the nozzle no longer has to hover above the wall; it can apply concrete from the side. Surfaces, however, become even more uneven. Another process being developed is particle bed 3D printing. It has the advantage that structures can be created freely within the printing space. The space is filled with a sand bed. Desired areas are glued with a suspension of water and cement, as with an inkjet printer. There, the particle bed solidifies. Printing takes place layer by layer. The advantage is that unbound particles remain in place and serve as a support structure for the print. Another approach is to print with sustainable materials. One example is Tecla , a building made from materials collected exclusively on site. The company advertises that this creates CO2-neutral mud huts made from fully recyclable materials that adapt to any climate and context.
Quellen:
https://www.youtube.com/watch?v=XhPrhlosmDo
https://www.unep.org/resources/publication/2022-global-status-report-buildings-and-construction
https://youtu.be/BNk3m8Y0aV8?t=3413
https://www.mae.ed.tum.de/cbm/ueber-uns/geschaeftsleitung/institutsleitung/gehlen-christoph/
„The realities of additively manufactured concrete structures in practice“
https://www.3dwasp.com/en/3d-printed-house-tecla/