Struktur, die Stabilität schafft
Der Architekt und Tragwerksingenieur Francesco Ranaudo untersucht, wie sich Betondecken dünner, leichter und nachhaltiger herstellen lassen. Dabei kommen 3D-Druckverfahren ebenso zum Einsatz wie die Techniken alter Baumeister.
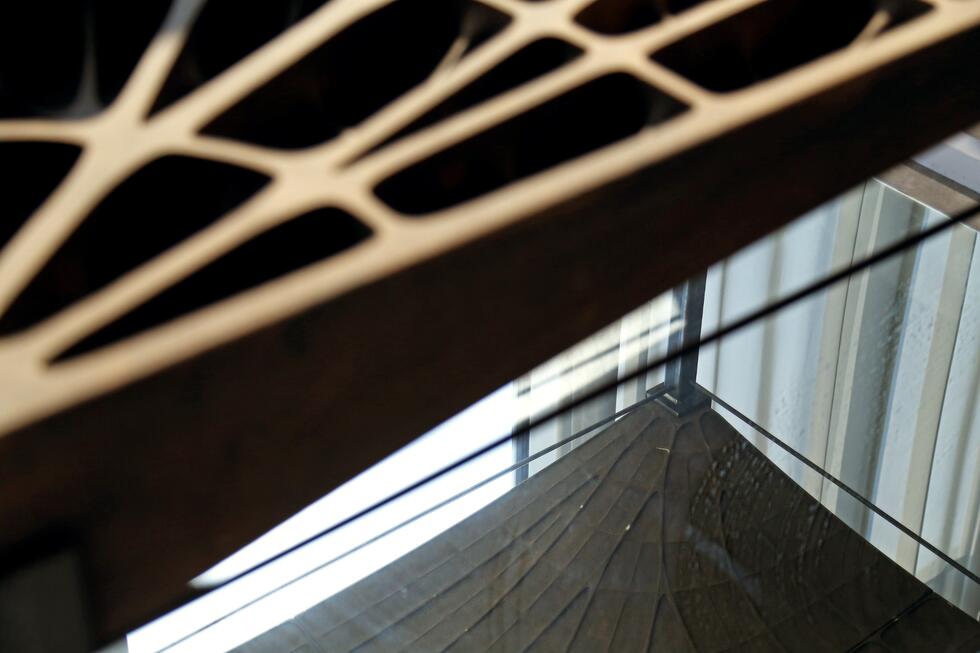
«Im Zusammenhang mit der Bekämpfung des Klimawandels denken alle zuerst ans Fliegen», sagt Francesco Ranaudo mit einem Kopfschütteln. Weniger zu fliegen schade natürlich nicht, räumt der gebürtige Italiener ein, der in der Schweiz an der ETH Zürich sein Doktorat macht. Aber die Architektur biete den deutlich grösseren Hebel, um die CO2-Emissionen einzudämmen.
Francesco Ranaudo erklärt: «Die Vereinten Nationen rechnen mit einem Bevölkerungswachstum von rund 2 Milliarden bis 2050. Um all diesen Menschen ein Dach über dem Kopf zu geben, müssen wir monatlich Wohnraum im Umfang von New York City erstellen. Ein neues New York – jeden Monat!»
Diese Rechnung macht deutlich, welche Wirkung flächendeckende Optimierungen haben. Hier will der Architekt und Tragwerksingenieur ansetzen. Als Doktorand am Institut für Technologie in der Architektur, als Forscher der Block Research Group und des Nationalen Forschungsschwerpunkts «Digitale Fabrikation» ist es sein Ziel, Baustrukturen zu verbessern und dabei Kosten und Emissionen zu verringern. Sein Fokus: Decken aus Beton.
Klimakiller Beton
Beton – ein Gemisch aus Wasser, Zement, Sand oder Kies – schadet der Umwelt. Ökologisch bedenklich sind unter anderem die Emissionen, die beim Brennen des Zements entstehen. Die Klimarahmenkonvention der Vereinten Nationen (UNFCCC) schätzt, dass die Zementproduktion für weltweit 5 bis 6 Prozent des menschengemachten Treibhausgas-Ausstosses verantwortlich ist.
Auch das Beimischen von Sand ist problematisch, weil es sich dabei um eine endliche Ressource handelt. Bei bewehrtem Beton kommen die Emissionen der Stahlproduktion hinzu: Je nach Quelle rechnet man dabei mit rund ein bis zwei Tonnen CO2 pro Tonne Rohstahl. Bei hohen Gebäuden, die aufgrund ihres Eigengewichts grösseren Kräften standhalten müssen, fällt die ökologische Komponente besonders ins Gewicht: ultra-hochfester, bewehrter Beton hat nämlich einen höheren Anteil an Zement und Stahl.
Eine bessere Ökobilanz hat Recycling-Beton, bei dem ein Teil der Gesteinskörnung – also des Sands oder Kieses – durch bereits bestehenden, zerkleinerten Beton ersetzt wird. Allerdings reduziert das die Belastbarkeit des Materials. Um gleichzeitig stabil und nachhaltig bauen zu können, braucht es folglich neue Konzepte. «Stärke durch Material» ist nach Meinung von Francesco Ranaudo nicht mehr zeitgemäss. Heute gilt: «Stärke durch Geometrie».
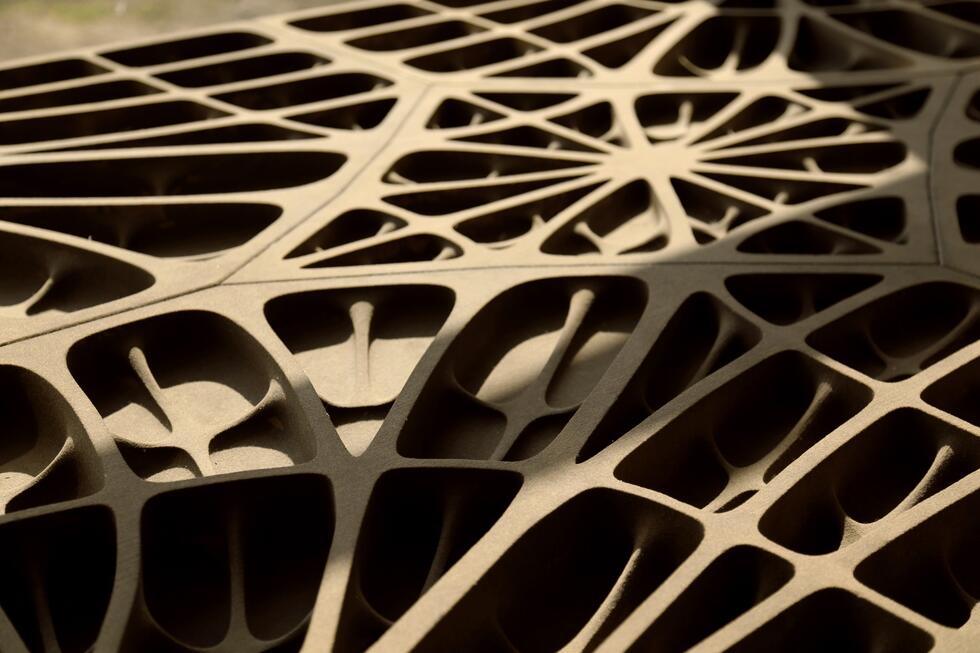
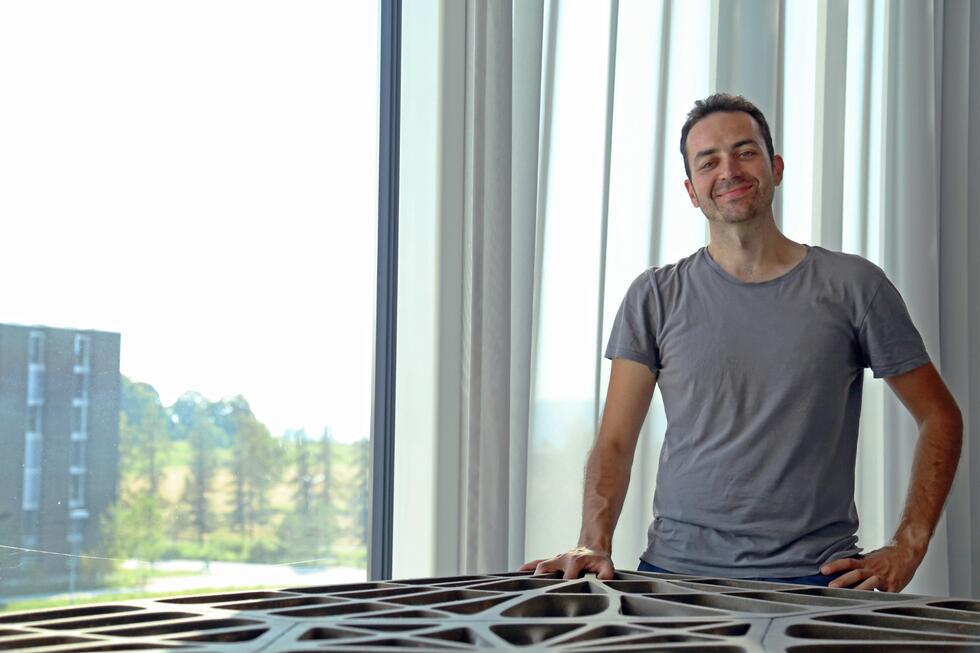
Von alten Baumeistern inspiriert
Was Francesco Ranaudo damit meint, zeigt er auf einem Rundgang durch die Räume des ETH-Instituts. Im Obergeschoss des Gebäudes steht ein Prototyp der Betondecke, an der er forscht. Mit seiner luftigen Rippenstruktur schaut das etwa fünf Quadratmeter grosse und rund zehn Zentimeter dicke Werkstück ein bisschen aus wie ein kunstvoll-verschlungenes Ornament einer gotischen Kathedrale. «Der Eindruck täuscht nicht, wir haben uns tatsächlich von den alten Baumeistern inspirieren lassen», sagt er. «Denn auch sie mussten die Stabilität ihrer Gebäude über die Form erreichen.» Die Möglichkeiten moderner Materialien kannten sie noch nicht.
Die Geometrie der Decke ist einerseits auf minimalen Materialverbrauch ausgelegt; andererseits bewirken die Rippenstruktur und eine leichte Gewölbeform, dass die Belastungen, die auf die Decke einwirken, sich gleichmässig verteilen und von der Mitte zu den Ecken abgeleitet werden. Kräfte, denen ein umweltfreundlicheres Material wie Recycling-Beton nicht standhalten würde, entstehen so erst gar nicht.
Folglich braucht es auch keine Armierungen im herkömmlichen Sinn. Lediglich an den Ecken der Deckenplatte sorgt eine Stützstruktur aus Stahl für weitere Stabilität. Also doch Stahl? «Ja», gibt Francesco Ranaudo zu, «aber wesentlich weniger als bei herkömmlichem Stahlbeton.» Hinzu kommt: Es handelt sich um eine externe Stützkonstruktion – nicht wie Armierungseisen, die im Beton eingegossen sind. Das macht es viel einfacher, das Material später zu trennen und wiederzuverwerten.
Dünner, leichter, ökologischer
Die Decke hält den Belastungen stand – selbst, wenn sie dünner und leichter konzipiert wird. «So sparen wir etwa 50 Prozent des Materials und zwischen 30 und 40 Prozent des Gesamtgewichts eines Gebäudes», erklärt der Forscher. Allein für ein grosses, 20-stöckiges Gebäude ist das Sparpotenzial enorm. «Ich habe das mal für einen Interessenten durchgerechnet», sagt Francesco Ranaudo. «Im Vergleich zu herkömmlichen Betondecken bräuchten wir mit unserem Konzept 1208 Lastwagenladungen Beton weniger. Und wir würden Armierungseisen in der Länge der Strecke zwischen Zürich und Brüssel einsparen – über 600 Kilometer.»
Dass die Decke nicht nur leichter, sondern auch dünner ist, wirkt sich umso mehr aus, je mehr Etagen ein Gebäude hat: Spart man rund 10 Zentimeter pro Decke ein, ergibt das ab 25 Stockwerken eine zusätzliche Etage – bei gleicher Gebäudehöhe. «Durch die Gewölbeform verlieren wir zwar wieder etwas Raumvolumen, aber das beschränkt sich auf die Ecken und Seiten – und dort hält man sich ja ohnehin eher selten auf», sagt der Forscher.
Wir würden Armierungseisen in der Länge der Strecke zwischen Zürich und Brüssel einsparen – über 600 Kilometer
Im Erdgeschoss des Instituts härtet gerade ein weiterer Prototyp der Decke aus. Viel sieht man nicht, denn die Platte steckt noch in ihrer Verschalung. Francesco Ranaudo erläutert die ausgeklügelten Details, die sich dahinter verbergen: «Die Rohre für Heizung und Kühlung sind direkt in die Platte integriert, so dass später keine zusätzlichen Installationsschichten nötig sind, welche die Decke wieder dicker machen würden. Zudem sind die Rohre so angelegt, dass möglichst viel Fläche für den Wärmeaustausch zur Verfügung steht.»
Auch die Belüftung wurden in Zusammenarbeit mit den Forschungsgruppen «Digital Building Technologies» und «Architecture and Building Systems» optimiert: Teile der Verschalung wurden im 3D-Druckverfahren hergestellt und geben dem Betonelement auf seiner Unterseite eine geriffelte Struktur. Diese Struktur erzeugt Mikroturbulenzen und verbessert so die Luftzirkulation.
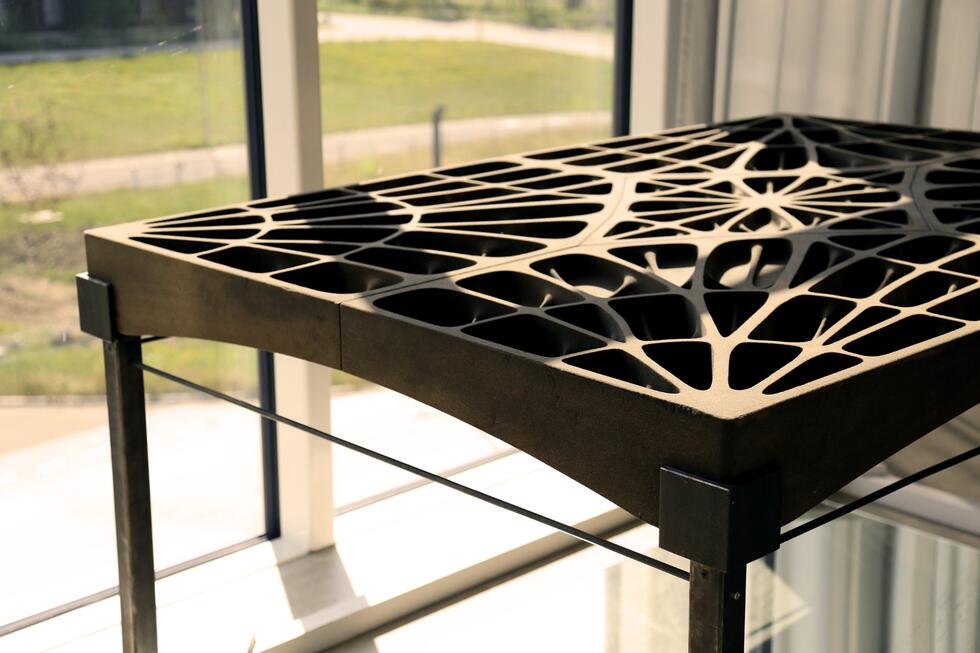
Auf dem Weg zur Marktreife
Ein erster Test des Konzepts steht unmittelbar bevor. Die Decke ist Teil des Projekts «HiLo» der Eidgenössischen Materialprüfungsanstalt Empa. Bei «HiLo» handelt es sich um ein zweistöckiges Gebäude in Dübendorf, das als Forschungs- und Innovationsplattform für neue Leichtbaumethoden dient. Mit dem Bau wurde im Sommer 2019 begonnen, im Laufe des Herbsts sollen die Decken eingezogen werden.
«Wenn wir uns an den Technology Readiness Levels der NASA orientieren, dann entspricht das Projekt ‘HiLo’ etwa dem Astronauten, der im Hallenbad trainiert – also Level 5 oder 6», erklärt Francesco Ranaudo. Um zu Level 9 – dem Maximum – zu gelangen, brauche es insbesondere noch Arbeit im Bereich von Zulassungen und Normen.
Und es sei absolut zentral, potenzielle Anwender sowie die breite Bevölkerung vom Konzept zu überzeugen: «Mit herkömmlichen Materialien und Prozessen kann man vergleichsweise einfach und schnell bauen. Das hat uns etwas bequem gemacht. Erst wenn Ressourceneffizienz genauso wichtig ist wie Zeit, wird sich daran etwas ändern.»
Digitale Fabrikation
Der von der Schweizer Regierung geförderte Nationale Forschungsschwerpunkt (NFS) «Digitale Fabrikation» untersucht innovative Planungs- und Bauprozesse in der Architektur – unter anderem mit dem Ziel, die Lücke zwischen den digitalen Technologien und dem physischen Konstruktionsprozess zu schliessen. Dabei geht es unter anderem um digitale Entwurfs- und Herstellungsverfahren und deren Synthese in neuartigen Technologien. Verschiedene Disziplinen arbeiten im NFS zusammen: Architektur, Tragwerksentwurf, Elektrotechnik, Maschinenbau, Robotik, Material- und Computerwissenschaften.
Fotografie und Text: