Revolution grüner Stahl
Die Stahlproduktion ist weltweit für acht Prozent der CO2-Emissionen verantwortlich. Es gibt alternative Herstellungsprozesse, doch die Investitionen sind hoch und der Weg weit. Zwei Experten geben Einblicke.
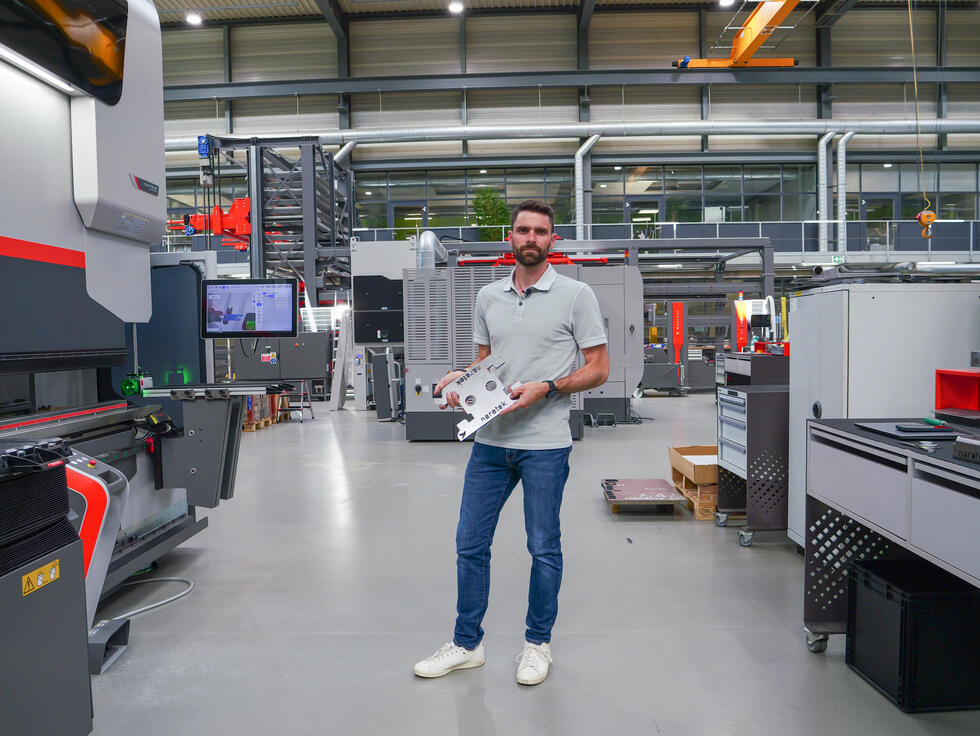
Unsere Welt ist auf Stahl gebaut. Von Gebäuden und Stromleitungen über die Automobilindustrie und den Schiffbau bis hin zur Medizinal-, Büro- und Computertechnik – kein Bereich unseres Lebens, in dem Stahl nicht in irgendeiner Form enthalten ist. «Stahl hat tausende Applikationen», sagt Wilfried Liegard, Mitglied eines Forschungsteams des Maschinenbauers Bystronic (siehe Kasten). Stahl biete so viele unterschiedliche Eigenschaften: Er kann ebenso starr wie biegsam sein, absorbierend oder federnd, einfach zu formen oder formstabil. Hinzu kommt, dass Eisenerz auf unserer Erde fast unerschöpflich verfügbar ist. «Auf Stahl ist unsere Welt gebaut», sagt er.
Und der Stahlhunger wächst: In den letzten 50 Jahren hat sich die Stahlproduktion rund versechsfacht. 2022 wurden laut worldsteel.org über 1,8 Milliarden (!) Tonnen Stahl produziert – zwei Drittel davon in China. Die Stahlproduktion hat deshalb einen entscheidenden Einfluss beim Erreichen der Klimaziele. Weltweit ist die Stahlproduktion für rund acht Prozent der CO2-Emissionen verantwortlich, in Europa beträgt der Anteil vier Prozent. Beim klassischen Herstellungsverfahren werden pro Tonne Stahl gleichzeitig 1,8 Tonnen CO2 erzeugt. Oder wie es Christian Leinenbach, Metall-Experte des Forschungsinstituts Empa und Dozent an der EPFL, spitz formuliert: «Eigentlich handelt es sich um eine CO2-Produktion. Eisen ist das nützliche Nebenprodukt.»
Dazu ein kleiner Ausflug in die uralte Methode der Eisenherstellung: Unter hoher Hitze wird Eisenerz in Kontakt mit Kohlenstoff gebracht – dies geschieht in Hochöfen bei Temperaturen bis zu 1'800 Grad.
Dazu ein kleiner Ausflug in die uralte Methode der Eisenherstellung: Unter hoher Hitze wird Eisenerz in Kontakt mit Kohlenstoff gebracht – dies geschieht in Hochöfen bei Temperaturen bis zu 1'800 Grad. Die Höllenglut weckt im Kohlenstoff den Hunger nach Sauerstoff, er bekommt ihn vom Eisenerz. Als Resultat bilden sich am Ende des Prozesses CO2, Schlacke und Roheisen. Um den restlichen Kohlenstoff aus dem Roheisen zu entfernen und Stahl zu gewinnen, wird in einem separaten Arbeitsschritt Sauerstoff eingeblasen. Dieser bindet den Kohlenstoff – weiteres CO2 und niederwertiger Baustahl entstehen. Um Edelstahl zu erhalten, sind Veredelungsprozesse nötig.
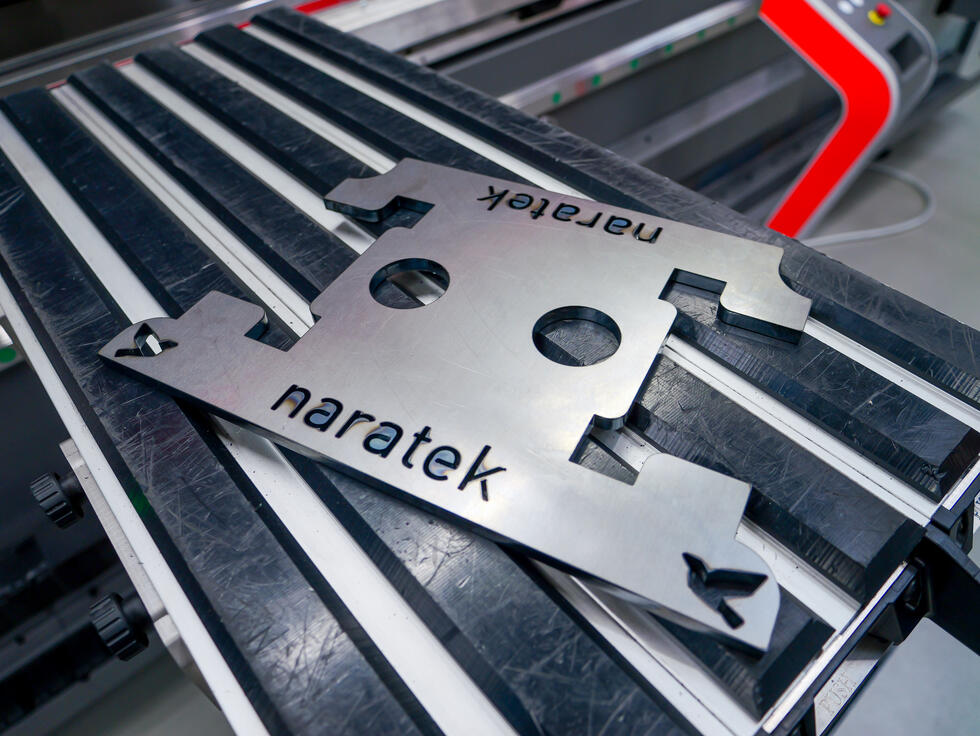
Ein zweites Verfahren trägt den Namen Elektrometallurgie oder Lichtbogenverfahren. Unter Verwendung von Grafitelektronen und Strom entsteht ein hochenergetischer Lichtbogen, der den Stahl schmelzen lässt. Das Lichtbogenverfahren funktioniert zwar weitgehend CO2-neutral, eignet sich jedoch nur zur Aufbereitung von rezykliertem Stahl und Schrott.
Biegt grüner Stahl anders?
Zurück zum Klimaschutz. Wie in anderen Lebensbereichen wächst auch in der Stahlindustrie der Druck, klimaneutral zu werden. Doch wie? Das Zauberwort heisst fossilfreier, respektive «grüner» Stahl – Stahl, bei dessen Herstellung möglichst kein CO2 in die Luft entwichen ist. Christian Leinenbach nennt mehrere Wege dahin. Einerseits kann der Sauerstoff dem Erz mit Wasserstoff statt Kohlenstoff entzogen werden. «Bei der Reaktion mit Wasserstoff fällt kein Roheisen, sondern ein poröses Granulat an», sagt er. Dieses kann anschliessend im Lichtbogenofen unter Stromeinsatz zu Stahl verarbeitet werden – der Energiebedarf ist dabei tiefer als jener des Hochofens. Wichtig ist: Der Strom für den Lichtbogenofen und die Herstellung des Wasserstoffs muss aus erneuerbaren Energiequellen stammen. Als zusätzliches Mittel auf dem Weg zur CO2-neutralen Stahlproduktion nennt Leinenbach Carbon-Capture-Technologien, wie sie beispielsweise vom Schweizer Startup Climeworks gebaut werden. Produziertes CO2 wird hierbei eingefangen und zum Beispiel im Boden gespeichert.
«Am Ende sollte die ganze Kette grün sein, inklusive der Transporte» Wilfried Liegard
Wilfried Liegard geht noch weiter: «Am Ende sollte die ganze Kette grün sein, inklusive der Transporte», sagt er. Wenn das Eisenerz in Indien geschürft, im Mittleren Osten zu Roheisen verarbeitet und in Frankreich zu Stahl verfeinert wird, belasten die Transporte des Materials das Klima zusätzlich. Auch die Minen müssten grüner werden, indem das Erz zum Beispiel mit Elektromaschinen geschürft wird. Nicht zuletzt müssten diese Maschinen selbst aus grünem Stahl hergestellt sein.
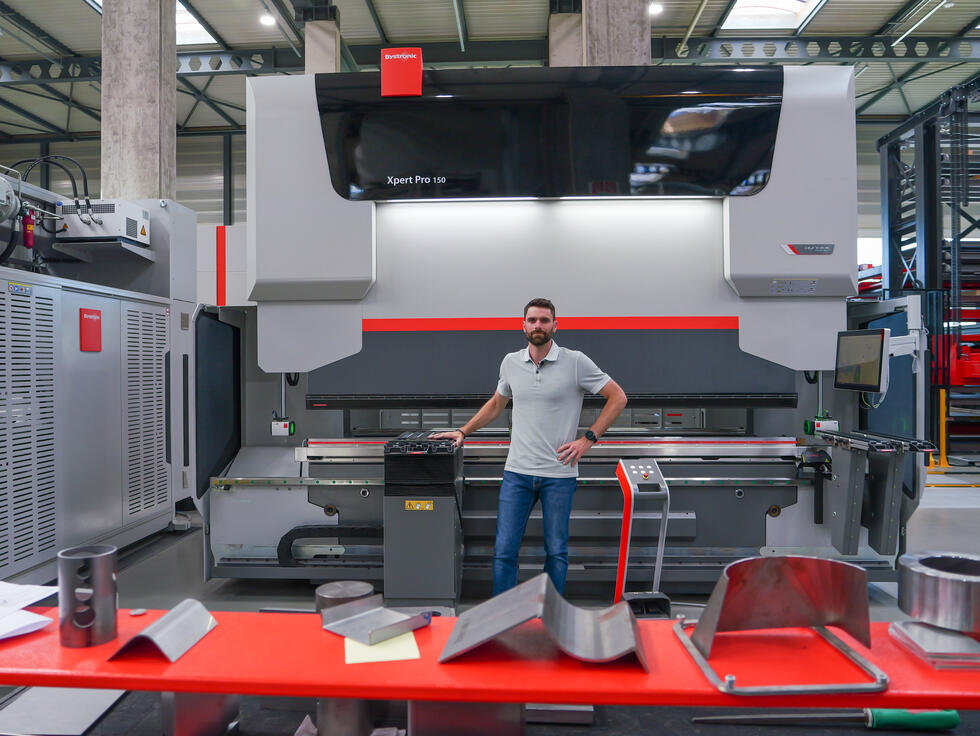
Für das Forscherteam bei Bystronic seien besonders auch die Materialeigenschaften von Interesse. Lässt sich grüner Stahl auf die gleiche Weise schneiden und biegen wie herkömmlicher Stahl? «Grüner Stahl ist chemisch und physikalisch praktisch gleich wie fossiler Stahl», sagt Liegard. Schneiden sei kein Problem. Beim Biegen hingegen stellten sich Fragen: Enthält der grüne Stahl beispielsweise grössere Reste von Wasserstoff? «Wir vergleichen Kurven und versuchen daraus zu schliessen, wie sich der Stahl bei unterschiedlichem Druck verhält», sagt er. Auch könne man nicht einfach von Stahl als Material sprechen. «Es existieren etwa 3000 verschiedene Stähle», ergänzt Empa-Forscher Leinenbach. Es handle sich um eine Stoffgruppe.
Milliardenhohe Investitionen
Noch wird grüner Stahl aber nicht in grossen Mengen hergestellt. Die Nase vorne hat derzeit das schwedische Unternehmen SSAB – mit einer Produktionskapazität von insgesamt knapp neun Millionen Tonnen allerdings ein kleiner Fisch im Teich: Der Stahlriese China Baowu Group produzierte 2020 über 115 Millionen Tonnen, Arcelor Mittal schaffte es auf 78,5 Millionen Tonnen. Dennoch ist SSAB wegweisend und hat zusammen mit Partnern das Projekt Hybrit ins Leben gerufen. Im schwedischen Luleå ist eine erste Pilotanlage mit Stahlproduktionsstätte und Wasserstoffspeicheranlage entstanden, der Strom kommt aus erneuerbaren Quellen. 2026 will SSAB den ersten fossilfreien Stahl auf den Markt bringen, bis 2030 soll die Stahlproduktion von SSAB weitgehend klimaneutral sein. Der grüne Stahl ist begehrt: Im Oktober 2021 stellte die Volvo Group das erste Nutzfahrzeug und 2022 den ersten Lastwagen vor, die mit (noch nicht kommerziell produziertem) grünem Stahl von SSAB hergestellt waren. Mercedes wird in einem ersten Schritt fossilfreien Stahl für Prototypenteile für Autos verwenden.
«Die grösste Herausforderung besteht in der Skalierbarkeit der Produktion» Wilfried Liegard
«Die grösste Herausforderung besteht in der Skalierbarkeit der Produktion», sagt Liegard. Der Wandel bedinge hohe Investitionen, er rechnet mit rund einer Milliarde US-Dollar pro Stahlkonzern. «Wir gehen deshalb von einer Verteuerung von Stahl um etwa 30 Prozent aus» sagt er. Leinenbach bestätigt diese Zahl und sagt es handle sich «um einen Balanceakt»: Die Autoindustrie beispielsweise müsse entweder den teureren Stahl in die Preisgestaltung fliessen lassen oder weniger Stahl verbauen. Einen gewissen Vorteil hätten Elektroautos, da sie keinen Motorenblock enthalten. Nicht zuletzt müsse man sich Gedanken zum Recycling machen, sagt er. Jede Tonne Stahl enthalte bereits heute etwa dreissig Prozent Recycling-Stahl, dieser Wert liesse sich verbessern. «Wir müssen den Werkstoff als Wertstoff betrachten», schliesst Leinenbach.
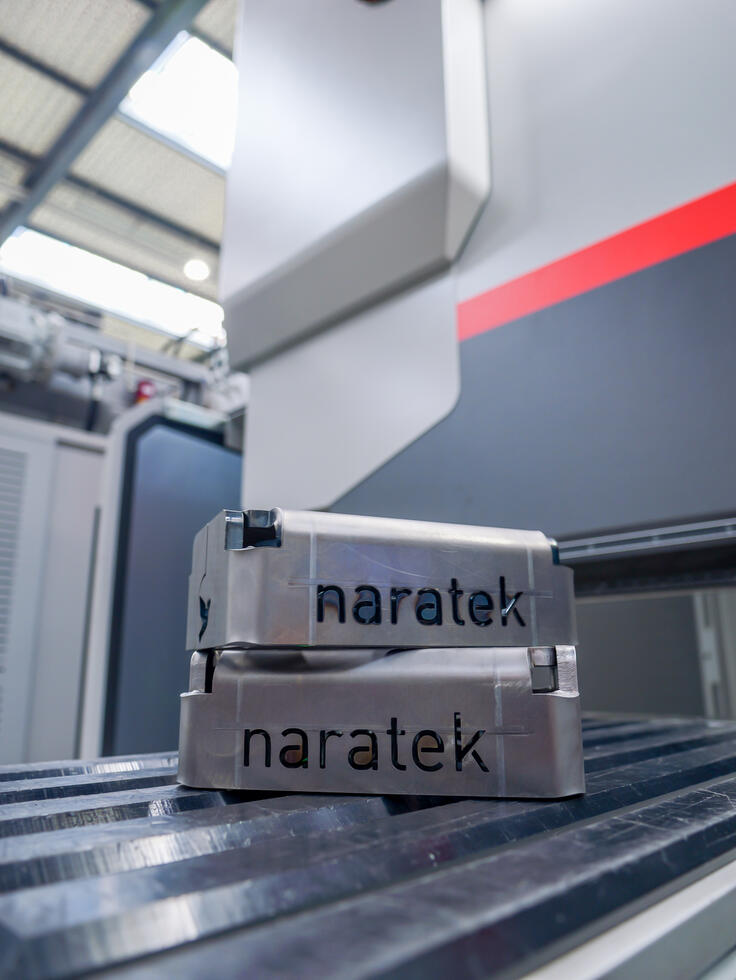
Forschung bei Bystronic
Das Forschungsteam von Bystronic wurde 2020 ins Leben gerufen und besteht aus elf Mitarbeitenden. Sie sind global tätig und beschäftigen sich vor allem mit Optimierungen für Schneidkopf-, Schneide- und Biegeprozessen. Wilfried Liegard, der bei Bystronic seine Doktorarbeit schreibt, untersucht dabei den Einfluss von Material und Maschinen auf die Prozesse. Aktuell untersuchen er und seine Kollegen spezifisch, ob und welche Auswirkungen fossilfreier Stahl auf den Biegeprozess hat.